440T load test using water weight bags in Africa
Client: Global provider of offshore marine services
Industry: Energy
Asset: Subsea support vessel
Location: Southwest Africa
Year: 2023
Challenge
A client required a load test of 440T on their crane, as part of a 5-yearly crane recertification campaign. The vessel was docked off the coast of Southwest Africa where the availability of high tonnage equipment is generally limited.
Solution
Axess Africa engineered a 440T load test rigging plan in cooperation with the client’s technical lifting authority. Once approved, its local supplier network was utilised to source the high tonnage water weight bags, shackles, slings and load cells required for execution.
The equipment was mobilised by road and air freight ahead of schedule to ensure the project was executed on time and within budget. A local team of highly experienced and qualified engineers were mobilised to prepare all the rigging works prior to executing the load test. They also performed non-destructive testing (NDT) on the crane, before and after the operations, to ensure structural integrity.
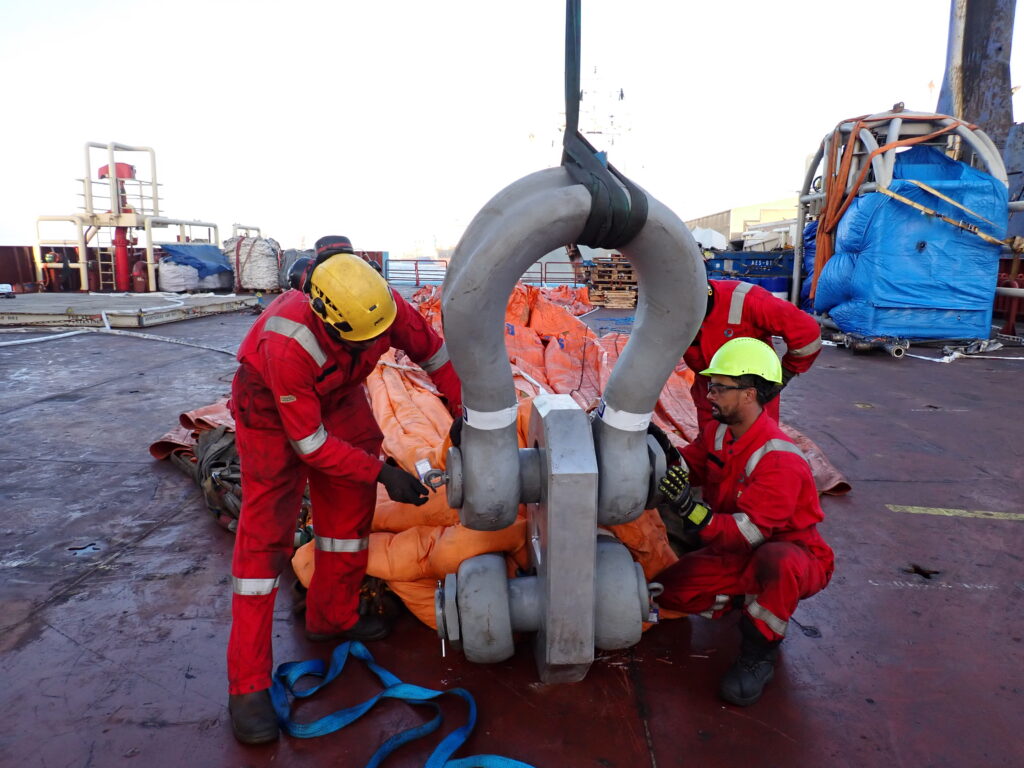
Results
The project was safely completed in two shifts within budget. It was witnessed and signed off by the Class technical authority.
Mobilising a multi-skilled team enabled Axess Africa to execute multiple scopes of work in addition to the load test, in a single trip, such as lifting gear surveys and eMAG wire rope inspection. The consolidation of tasks reduced mobilisations, resulting in cost savings and decreased greenhouse gas (GHG) emissions. This approach also helped the client in simplifying the administrative process of finding and coordinating with multiple vendors. Using local personnel eliminated the need to mobilise personnel from abroad, which would have incurred additional accommodation and travel costs and increased GHG emissions.
Jeff Davenport, Project Manager at Axess Group, said, “Besides performing the 440T crane load test, we also performed load tests on smaller cranes and lifting machinery, including all the pre and post-NDT, and conducted lifting gear surveys, phased array inspection on slew ring bolts, eMAG wire rope inspection, and more. We are thankful to our client for the successful cooperation on this project and look forward to supporting them in their next campaign.”
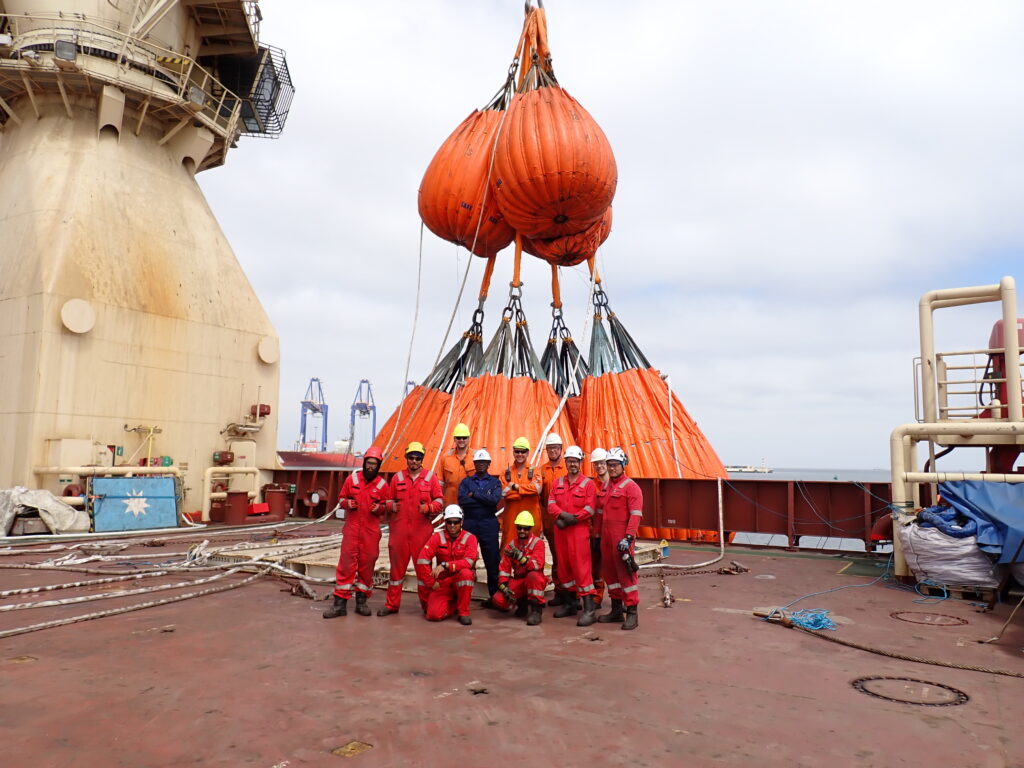